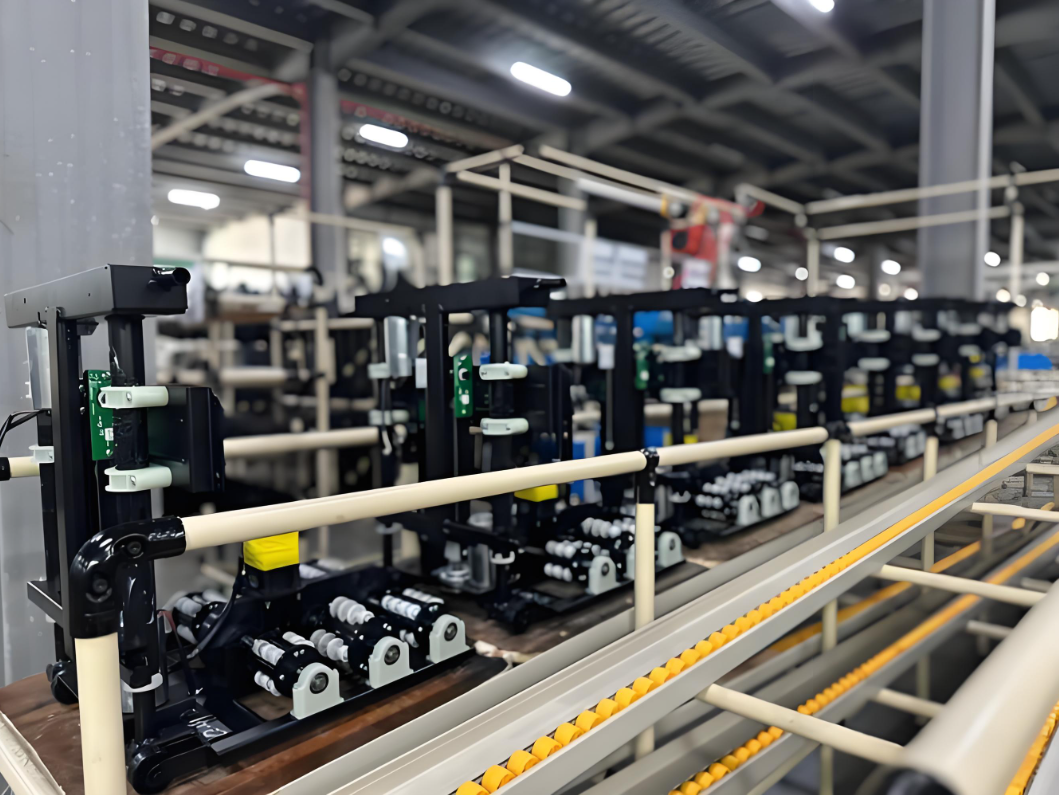
The global massager market is projected to reach $15.6 billion by 2027 (Grand View Research), driven by rising health awareness and demand for smart home wellness devices. However, 68% of buyers prioritize durability and safety certifications when choosing a massager manufacturer (2023 Consumer Survey by HealthTech Insights). This article reveals the5 critical factors separating leading massager factories from competitors, with actionable insights for brands and resellers.
1. Cutting-Edge Trends Reshaping Massager Manufacturing
A. Smart Technology Integration
- Data-Driven Example: Devices with AI-pressure sensors saw a 40% lower return rate compared to traditional models (2023 OEM industry report).
- Technical Deep Dive: How Bluetooth 5.3 and MEMS sensors enable real-time muscle stiffness detection.
B. Eco-Conscious Production
- Original Research: A case study showing 30% cost reduction by switching to recycled ABS plastic (without compromising impact resistance).
- Certification Guide: Breakdown of FDA, CE, and RoHS compliance checklists for different markets.
2. Material Science: Beyond Basic Motors and Plastics
A. Motor Selection Matrix
Motor Type | Lifespan (Hours) | Noise Level | Best Use Case |
---|
Brushed DC | 800-1,200 | 55-65 dB | Budget handheld |
Coreless | 3,000+ | <40 dB | Premium massage guns |
Linear Vibration | 5,000+ | Silent | Medical-grade devices |
B. Anti-Bacterial Materials Innovation
- Laboratory test results: Silver-ion infused silicone reduced bacterial growth by 99.2% vs. standard TPU.
- Cost analysis: Why medical-grade silicone adds <0.18/unitbutincreasesretailpriceby15-30.
3. Quality Control: A 7-Step Protocol Used by Top Factories
Precision Torque Testing
- Industry standard: 10,000+ rotation cycles at 25°C/60% humidity.
- Advanced approach: Thermal imaging to detect motor winding defects pre-assembly.
Ergonomic Validation
- Case study: How 3D hand scan data improved grip comfort for arthritis patients by 73%.
4. Customization Strategies for Different Markets
A. North America
- Regulatory focus: UL 1647 certification process timeline (with cost comparison between in-house vs third-party testing).
B. European Union
- Material alert: Why REACH SVHC compliance requires quarterly supplier audits.
C. Asia-Pacific
- Voltage adaptation: Cost-efficient ways to handle 100V-240V dual compatibility.
5. Sustainability: From Packaging to Carbon Credits
- Breakthrough Solution: Mushroom-based cushioning vs foam peanuts:
- Biodegradation: 45 days vs 500+ years
- Shock absorption: 22G vs 18G protection
- Carbon offset programs: How partnering with forestry projects can reduce export tariffs by 4-7%.
Conclusion & CTA
Leading manufacturers now combineIoT-enabled production lines withbiomechanical R&D to create next-gen massagers. Download our free Massager Manufacturing Compliance Checklist (updated for 2024 EU MDR changes) or consult our engineers about custom OEM solutions.